第五章 使用绩效数据
对应大纲内容
2.2分析用以改进供应链的主要统计方法的应用
· 为绩效测量整理数据
· 制定用于供应绩效的关键绩效指标(KPIs)
·分析统计数据
· 正态分布的应用
· 实施统计过程控制
· 六西格玛改进方法
· 持续改进
CIPS中文课程学习社区编辑整理-国内最Open的CIPS学习资源社区
更多学习资源可访问www.szcps.net或微信公众号:szcips
引言
在上一章关于质量管理的论述中,我们讨论了持续改进、过程控制和过程改进对于取得全面质
量的重要性。本章我们进一步探讨绩效测量(用以过程控制)的相关主题和过程改进。我们特别关
注应用定量数据和统计技术来测量和改进供应链绩效。
我们首先论述供应链中绩效测量的使用,如何为供应链的不同方面制定关键绩效指标(KPIs),
以及如何收集绩效数据和反馈。我们还将概述过程控制和改进的其他方法。
随后我们将讨论如何分析绩效数据,应用统计技术指出需要处理的偏差、风险和不利的趋势。
在考试中,也许会要求你针对一个案例中的数据进行这类基本的分析。更广泛地讲,你应当准备解
释统计技术在过程控制与改进中的应用。
最后,我们介绍统计技术在过程控制与改进中的多种应用,包括统计过程控制和六西格玛。
第一节绩效测量
供应链中的绩效测量
1.1 供应商绩效测量是将供应商当前的绩效与如下各项进行对比:
· 已定义的标准绩效(例如KPI或者服务水平协议),以确立是否实现了目标绩效或议定的
绩效水平;
· 以前的绩效,以发现趋势是恶化还是改善;
· 其他组织(供应商、采购职能)的绩效或者标准标杆,以便找出与最佳实践标准或者竞争
对手相比还差在哪些地方,什么地方还可以进一步改进。
1.2绩效测量很重要,因为它们有助于运作与关系的计划与控制:我们常常说“对什么进行了衡量,
才能把什么管理好”。通过找出供应商目前的绩效与期望的或竞争对手的绩效、或与最佳实践
之问有差距的地方,会促使绩效得到改进,供应商因而获得发展。这是一种重要的沟通工具,
可以和利益相关者就他们应该在供应链绩效中发挥什么样的作用及目前做得如何等进行沟通。
绩效测量指标,例如KPI(关键绩效指标),可以被用来管理、激励和奖励个人、团队及供应
商。
1.3供应商绩效评估(或者供应商等级评定)可以:
· 帮助识别质量最好或绩效最佳的供应商:帮助做出下列决策:①哪个供应商应当获得特定
订单;②什么时候供应商应该在批准的或首选的供应商清单中被保留或被剔除;③和哪个
供应商有可能建立更具战略性的合作关系;及④如何在几个供应商中分配某项采购资金以
便更好地管理风险。
· 显示应该如何或者是否需要处理与供应商的关系,以提高或改进他们的绩效(例如:评估
采购活动中供应商选择及合同管理流程的有效性)。
· 帮助确保供应商履行合同中的承诺。
· 激励供应商保持及,或不断提高绩效水平。
· 通过找出可以消除或改正的问题,以及供应商需要哪些支持或提升,从而极大地提高供应
商绩效。
1.4 当然,关于采购方的采购与供应链绩效也有类似的考虑。采购方对于他们自己政策、做法和
绩效在供应链有效性和效率方面的影响应当保持警惕,这一点很重要。各种改进方案很可能
在关注供应链绩效测量与调整之前或之中,集中于采购绩效的测量与调整。
关键绩效指标(KPI)
1.5 关键绩效指标(KPI)是一些清楚的定性的或定量的说明,它定义了在一些关键领域(或对
于一些重要的成功要素)适当的或期望达到的绩效,对照这些指标,可以对进展及绩效进行
测量。关键绩效指标的要点在于,通过现有的数据收集系统,这些指标所表述的绩效目标或
者期望值,为我们提供了一种可以直接对操作层面的绩效进行细致的、一致的测量方式。
1.6 只要可能,这些目标都应被定量,也就是说是数宁化的、统计上的。它们可能表示为成本数
额(例如提供每次服务的成本,成本节约的数量)、时问长度(例如每次服务所用的时间)、
产出的数量(例如每年完成的项目数,每月交付的数量,所提出的缩减成本方案或创新提案
的数量)以及其他统计数据(例如足量按时交付的产品的比例或百分比,或每一评审期内收
到的投诉数量)。
1.7 不过,有些目标,也可能是比较“定性的”,也就是说是主观的,与质量或性能相关却无法简
单地进行定量,所依据的数据也不是那么成系统(例如客户调查)。举例来说,你可能会希
望评估客户满意度、供应商客户管理的效率,响应能力以及对于质量所做的努力,或者企业
社会责任。尽管如此,这些领域的关键绩效指标也应该尽可能做到定量:例如客户对服务表
示满意的比例和不满意的比例;客户表示满意的程度(使用评级或打分方式);客户提出要
求以及商家做出反馈的比例以及迅速程度;通过对态度进行调查,对企业在质量上的努力程
度进行打分;严重事故的数量以反映人员是否负责任等。
1.8 有效的绩效测量指标及目标常常用其英文首字母缩写"SMART”来表示。
· 明确的(Specific):清晰、明确、精确地表述期望达到什么样的结果或取得什么样的
成果,这样合同各方就能清楚地知道自己应该努力做到什么,对什么负责。
· 可测量的(Measurable):可以加以监控、审查及测量(最好能以定量的或数字化的方
式来表达),因此各方都可以有效地对进度和成果进行测量。
· 可实现的(Attainable):可实现的、现实的、具有合适的时间及资源。即使目标得到“延
展”或为了刺激改进,所要求的绩效水平也必须是可实现的。
· 相关的(RelevarIt):绩效测量指标应该和组织的战略目标、采购职能部门的政策及目
标、组织及供应链的关键成功要素以及商业需求相关并相符。
· 有时间约束的(Time-bounded):给出了完成(或评审)的确定时间表及截止日期,
而不是无限期的。
1.9 也有一些版本的"SMART,,增加了下列各点:
· 延展的(Stretching):绩效测量指标应故意设计成具有一定的挑战性,以激励供应商
使他们达到一定的绩效、持续学习、发展和改进(例如:作为供应商发展或持续改进
协议的一部分)。
· 可持续的(或者负责的)(Sustainable):关键绩效指标应根据部门(或组织)对关键
利益相关者应负的道德责任,考虑到对他们可能带来的影响。
· 同意的(Agreed):写入合同、协议或章程中(正式的或非正式的),以确保共同努力
及承担责任。
· 有奖励的(Rewarded):实现了关键绩效指标就可以获得某些激励或奖赏,作为绩效
管理及供应商激励程序的一部分。
· 审核的(Reviewed):应对关键绩效指标进行阶段性审核,以便在环境或者要求发生
变化时对它们进行及时的调整,或者可以把指标设计成“渐进式”的,以便持续地提高。
关键绩效指标在绩效改进中的优点及局限性
1.1 0使用关键绩效指标(对于采购与供应链职能以及供应商)具有如下优点:
· 提高及改进关于绩效事宜的沟通(关注结果的)。
· 激励实现或改善特定绩效水平(特别是运用与关键绩效指标相关的激励、奖赏或惩罚
措施)。很多情况下,设定了清晰的目标,激励的作用就会更强。
· 通过整合的或双向的绩效测量(用关键绩效指标来衡量供需关系双方的绩效),推动采
购方和供应商的协作关系。
· 可以进行直接的年度绩效比较,找出改善或恶化趋势。
· 关注关键结果(即关键成功要素),例如成本降低及质量改进。
· 明确地确定共同的目标,促进跨职能及跨组织的团队工作及关系。
· 减少由于目标混乱或期望值不明确可能导致的冲突。
1.11对供应商绩效设定关键绩效指标会在下列方面对供应链改进带来益处:
· 设定明确的绩效标准及期望值:激励完全实现目标并不断改进。
· 管理供应风险:控制质量、交付、资金价值等等
· 支持合同管理(确保获得协定的收益)
· 找出绩效水平高的供应商,以便列入批准的或首选的供应商名单(这反过来可以帮助
用户部门提高采购效率)。
· 找出有可能与之建立更密切的合作伙伴关系的高绩效水平的供应商。
· 提供反馈,以便不断学习并持续改进采购方与供应商的关系,这对供应商和采购部门
都是有益的。
1.12值得注意的是关键绩效指标也有缺点。追求实现某一关键绩效指标可能会导致某些不当的或
次优的行为,例如,为达到生产效率或时间目标而在质量或服务上偷工减料,或者某个部门
为了实现自己的目标而不惜破坏跨职能的协作或协调关系。因此在设定目标的时候就需要考
虑到这一切并谨慎为之。
设定关键绩效指标(KPI)
1.13对于某些常规的合同及一般的采购,组织可以采用标准的关键绩效指标或绩效测量体系。不
是在任何情况下都需要制定系统的关键绩效指标并进行严格分析的。事实上,对于低价值的
常规采购来说,这样的流程从成本收益分析的角度看是不值得的。但是,对于复杂的、高价
值的、全新的采购合同及项目,就有必要采用系统的流程去开发适合的绩效测量体系。
1.14下面总结了一个制定关键绩效指标(KPl)的简单程序,详见图5.1。
图5-1 制定关键绩效指标
1.15有一点很关键,就是必须使供应商的关键绩效指标与商业需求及采购目标相一致,同样这些
也必须与企业的目标及供应链的关键成功要素相一致。
1.16对一个合同,无需确定过多的关键绩效指标,只需找出那些衡量关键成功要素的指标。否则,
监督及测量绩效会太过复杂,成本会太高,对于供应商来说,要达到多项关键绩效指标也会
太过复杂和艰巨。对于任何一个计划和控制的时间段,设置8到10个考虑周全的关键绩效
指标是比较现实的。
1.17在制定KPI时,有效的沟通交流是必须的。采购者应当明确告知供应商期望达到的绩效标
准。可以根据最近的历史数据(如果有的话)来反映趋势,并辅以对关键事项及要求的书面
解释说明。对于复杂的价值高的新采购合同,值得付出努力的那种,采购者应该让供应商参
与进来,和他们一起制定KPI,而不是等到KPI确定下来之后再通过谈判来讨论接受还是不
接受。在制定指标的过程中,供应商可以发挥自己的专业知识和经验。而且,这种经共同讨
论确定的指标会使供应商更容易接受,促使他们全力以赴达到指标。
供应商绩效测量指标示例
1.18过去,供应商绩效测量指标基本上都是和操作层面的绩效状况相关,主要关注成本、质量、
客户服务水平、交付等指标。这些方面显然非常重要,但它们在某种程度上是单维度的和回
顾性的。近年来,企业更加关注取得长期的、可持续的竞争优势,对供应商的评估越来越多
地考虑他们的整体供应链能力、响应性、创新等等。
1.19表5.1列举了部分可应用于各个不同层面的绩效测量指标:
表5.1 用于不同层面的绩效测量指标
1.20采购方可能会希望对供应商绩效的一些关键成功要素进行评估。每个要素都可以选出一些相
应的关键绩效指标。在考试中,就像在采购职业实践中一样,你显然需要选择或设计出那些
与合同内容及类型(如果已经在问题中明确的话)最相关的关键绩效指标。对于一般的供应
合同,主要应对表5.2中所列关键成功要素的绩效测量指标进行分析。
表5.2供应商绩效的一般性关键绩效指标
为绩效测量收集数据
1.21绩效监控(对照关键绩效指标来查验进展情况和绩效水平)和审核(对计划期间内的绩效进
行的回顾)的方法有若干种。
·有些时候我们可以进行持续监控:比如说有一些电子监控设备,我们可以给其设定一定的
参数或公差值,当监测结果(如产出率、成本或准时足量交货比例)超出了计划水平的时
候它们就会给出偏差报告。
·更普遍的情况是在过程、项目或合同的一些关键阶段进行绩效监控,例如在项目各阶段结
束的时候,或在生产或交货限期来临之际。
·阶段性的审核很常见:定期对照预定测量指标或阶段目标来检验成果。这种审核的目的通
常是调整性的,也就是在绩效水平或计划尚有调整余地的时候提出反馈信息。举例来说,
买方可能会定期抽取一个供应商的加工产品,检验其质量以及是否符合规格要求;买方和
供应方的团队可能定期会面讨论合同履行中的各种事宜。
·对于项目和合同的完成后审核通常是为了交流反馈意见、吸取经验教训以备将来改进。
1.22有很多种形式的反馈机制,可以用于收集供应商绩效数据并与相应的绩效测量指标相比较。
至于具体选用哪一种则要看所需的是定量的还是定性的数据,以及评估的是绩效的哪个方面。
下面略举几例。
·通过小组座谈、投诉处理、调查问卷以及项目审核的方式从内部和外部客户以及其他利益
相关者处收集反馈信息。
·通过观察、测试(如质量检验)、以及对文档、交易记录、管理报告(如质检报告分析等)
的分析等方式搜集绩效信息。
·预算控制:对照预算或者成本预测来监测实际成本。
·正式的绩效审核或评估(有时也称为供应商等级评定):根据对比标杆、关键绩效指标以
及双方认可的服务标准对绩效进行审核,并将这些信息反馈给改进计划。
·合同管理,依照合同条款持续性地进行合规性监控。
· 买方和供应方代表(或项目经理与客户经理)定期会面核查总体进度情况或处理一些具体
问题,例如费率、交货问题等,并就进展情况交换反馈意见。
·项目管理:在项目的关键阶段完成或里程碑处报告情况、举行会议;项目经理定期提交情
况通报;完成后审查与报告,目的在于为以后的项目汲取经验。
·聘请顾问来监控是否达到质量标准、标杆水平或伦理标准(如海外供应商的工人待遇)。
·如果买方不具备相应的专业知识,可以请技术专家来监控供应商绩效(如关于基建或lT
项目)。
供应商等级评定
1.23系统性的合同后绩效评估和评价常常称为“供应商等级评定”(Vendor rating),这里的“供应
商”是指目前卖给你东西的个人或组织,而等级评定”是指一种评估方法或对绩效“打分”。供
应商等级评定就是根据双方商定的标准测量供应商的绩效。
1.24供应商等级评定的一种常用的方法是使用供应商绩效评估表,即一份关键绩效要素的检查表,
供应商经理对照该表将供应商绩效评估为良好、满意或不满意。对每个要素赋予一个权重,
就可以将关键绩效领域的供应商绩效归总为良好、满意或不满意。一旦制定出有意义的检查
表,则这种方法易于实施,但它比较宽泛和主观。
1.25另一种方法是要素评级法(Factor rating method),或加权系数记分卡系统,即对每个关键
评估要素打分。这种方法对每个主要因素赋予一个数字权重, 向供应商(及其后续绩效评
估者)表明哪些绩效测量指标对于完成商业需求和目标最为重要,以及如何“分解”评判它们
的绩效。
1.26例如,质量绩效测量可能是“100%减去总交货中拒收的百分比”,如果一个供应商的送货中有
3%拒收,那么该项测量指标的分值为97%或0.97。每个主要要素也会根据其在整体绩效
中的重要性被赋予一个权重,并被用于每个分数,最后得出一个总体分数或评级,见图5.2。
图5.2要素评级法
1.27在这个范例中总分是1而供应商得分为0.908。我们可以把这个分数拿来和其他供应商作对
比,这样一来谁高谁低就清楚了。我们也可以作年同比,看某位供应商的绩效是逐年提高还
是逐年降低。
1.28图5.3是一个简单的绩效测量记分卡示例。
图5.3加权供应商记分卡
1.29很显然,这两种供应商等级评定法都不能告诉我们导致绩效低下的原因,也不能告诉我们如
何才能解决这些问题。所以还是要把供应商等级评定放在整个绩效管理过程中来看,见图
5.4。
图5.4供应商等级评定
第二节统计学简介
2.1有两大类统计学方法:
·描述统计学(Descriptive statistics)是指以可理解的和有用的形式呈现统计数据,包括使
用表格、图表和图示来表现统计信息。本课程大纲中没有明确提出数据的呈现,但我们将
提到过程测量与控制中使用的一些图示法。
·推断统计学(nfereritial statistics)是指分析统计数据的方法,用以对所讨论问题推导出
相关结论。这是绩效测量和控制的主要关注点。
统计抽样
2.2很多情况下,一个给定数据集中数据的“总体”(Population)很大:出于现实的和成本有效的
目的,检验和分析将集中于精心结构化的样本,该样本①足够大,能够代表整体;②真正代
表整体,因此关于该样本的结论可以延伸到整个总体。
2.3在统计质量控制中,常常使用概率抽样法,借此总体中的每个个体都能够被选作样本的一部
分。
·在简单随机抽样中,抽样者使用一个随机数发生器从总体中选择对象,如果发生器产生出
3和175,则第3和第175个对象被抽样。
·在系统抽样中,我们从总体中选择每个第n个对象。例如,如果我们想在总体为1000个
对象中抽取40个样本,可以选择每个第25个对象。
·在分层抽样中,使用与所研究对象相关的任何一种分类,将总体分为不同的类别。对每一
类别,我们选择一定数量的对象,加入我们的总样本中。通过这种方法,我们试图使样本
更好代表总体。这种方法的变体是定额抽样。
·在整群抽样中,不是抽取单个对象,而是抽取对象群。比如,如果总体是由某个城镇的居
民构成,可以将该城镇分为1000个区,每个区10栋住宅。那么样本可以由很多这样10
栋住宅一组的群组构成,这要比选择单个住宅快很多。
·在多级抽样中,为抽样逐渐进行细分。例如,如果总体是英国的每个个体,我们可以指定
区域,在每个区域中选择一定数量的有代表性的县,将每个再细分为更小的区,然后使用
整群抽样法来生成样本。
2.4本章讨论的大多数统计质量控制技术都是使用过程输出的随机样本或系统样本,而不是100%
检验。
平均数
2.5统计学的主要目标之一是总结大量数据,使其重要特征变得显而易见。一种方法是用中心位
置量数(通常是指平均值)以中值代表和总结数据。有数种方法确定一个数据集的中点,每
种方法各有其优缺点。
2.6算术平均数(表示为 )是最常用的平均值。它是所有各项之和除以项目个数,例如,3、
6、10、14、17、19和22的算术平均数可以计算如下:
X的平均数 =(3+6+10+14+17+19+22)/7=91/7=13
2.7这一计算很简单。它用到了该数组中的所有数据,因此提供了在数学上的精确值用于更高级
的数学统计。可是,它对极端项(即高的值和低的值)可能赋予不适当的权重,所得平均值
可能与数组中的任何项都不相符(比如“平均”家庭1.8个孩子)。
2.8一个数组中,如果所有项按量值大小排列,可以计算出中值。如果数据个数是奇数,则中值
即为中间一项的数值。如果数据个数是偶数,则中值是中问两个数据的算术平均值。例如:
·一组数值3、6、10、14、17、19和22,共有七个数据。中间一项的值是14,故中值即
为14.
·如果在数组中再加上25,数组有八个数据,则中值是两个“中间数值”(14和17)的算
术平均值,即(14+17),2=15.5。
2.9 中值不难理解,它不受极端值的影响:将最后一项数值改为50或1 00不会影响该数组的中
值。在不知道极端值的情况下也可以计算出中值,且不受数据不等组距或端尾开放的影响。
缺点是如果只有少数几项数据,平均值也许不具真正的代表性,不适合用于数学统计。
2.10众数是在数组的所有数值中最频繁出现的数值,它通常可以凭观察来确定,无需计算。然而,
一个数组可能有一个以上的众数,也可能没有众数。例如,抽样1 1个过程输出测量值:7、
7.5、6、6、7、5、6、5、6、5和5 cm。众数是5和6(每个发生了四次)。
2.11 众数不难理解,不受极端值的影响。即使数组中不是所有值都知道,也可以计算出众数。其
缺点是可能没有众数,目.众数值可能不适于数学统计。
离差测量
2.12一个数组的平均值或中点本身并不能很好传达数组分布的情况。如果你被告知一条河的“平
均”水深为1.5米,在你试图趟河而过之前你也许想知道样本测量数值实际上是否在0至25
米之间变化1
2.1 3换言之,数值可能密集集中在中点周围,也可能分散在很宽范围内。数组或分布的这一方面
称为分散程度或离散性。一起使用平均值和离散度,特别是结合算术平均和标准差,为我们
提供了一种有力的预测工具。
2.14离差测量提供了计算一个单一数字来测量数组中各项分散程度的不同方法。在此我们考虑两
种特别的测量指标:全距和标准差。
2.15全距(Range,也称极差)是离散性的最简单的度量,是一个分布的极值之间的差:即最
高值减最低值。例如,3、6、10、14、17、19和22的全距是19(22—3)。
2.16全距无法给出最低值与最高值之间数据的离散信息,因此只能在基本的质量控制中度量离散
度(要求快速计算),此外没有太大的使用价值。全距对于整体数据没有代表性,并且如果
数据中仅仅包含一个特别高的或特别低的值,全距会带来误导。
2.1 7标准差(Staridard deviation)是度量离散度的一个很有价值和应用广泛的指标。然而,它
的计算较复杂。本质上讲,它是计算一组数据偏离其平均值的平均距离。因此,如果一个发
布中的所有数据项都紧密聚集在算术平均值附近,则它们离平均值的平均距离很小,即标准
差很小。如果各数值很分散,则它们离平均值的平均距离较大,即标准差较大。
2.18标准差(也表示为希腊文西格玛,即σ)是对一组数据使用软件的计算器、计算表格功能
或其他统计软件进行计算。例如,一组数据抽样包括五个数据点:6.5,。7.5,8.0,7.2和6.8。
·全距是最高值减最低值=8.0—6.5=1.5
·算术平均值( )=(6.5+7.5+8.0+7.2+6.8),5=7.2
·标准差(σ)=O.59(你不必知道这是如何计算出来的)
统计概率论
2.19概率的一般概念是确定一个事件“可能”或“不可能”的程度。统计概率是在数学上度量这
种“可能性”的程度,以便基于现有证据和计算出的风险进行商业决策。概率以0至1之间
的数字来衡量,0代表不可能而1代表必然。50:50的机会可以用数值O.5表示。
2.20概率的经典定义是,一次试验中事件A所有可能出现的结果的总数目为m,事件A在试验
中实际出现的结果数为n,则事件A的概率P(A)为n/m。
例如,一个很方正的骰子以不偏不倚的方式投掷,则得到1至6分的可能性是均等的。这些
分数中的三个是偶数(2、4或6),因此偶数得分的概率是3/6,即1,2。我们可以将此表示
为数学式:
P(偶数)=3/6(即1,2)。
2.21 概率论的主要应用之一是解释随机样本(例如一个流程的输出)的结果。根据定义,一个样
本总体的所有个体被包含在一个随机样本中的可能性都是均等的,因此概率的上述定义适用
于随机抽样理论,也是这里要使用的。
2.22两个或多个事件也许是相互排斥的,即只有它们中的一个发生(例如在单次投掷骰子中的“得
分6”和“得分3”)。
·互斥事件可以表示为:P(A与B)=O。两个事件同时发生的概率为0.
·可是,在一次给定的试验中事件A或者事件B发生的概率是二者概率之和(相加):P(A
Or B) =P(A)+P(B)。
2.23对于两个或多个事件,如果一个事件发生或不发生的概率不影响另一个事件发生或不发生的
概率,则将这些事件称为独立事件。例如,考虑事件A(质量缺陷)、事件B(与通过了质
量认证的供应商建立合同关系)和事件C(引入电子P2P采购)。如果B发生了,则A发生
的概率会降低,因此A与B相关。另一方面,事件A和C相互没有直接的影响,因此它们
是相互独立的。如果任何两个事件A和B是相互独立的,则事件A和B同时发生的概率是
其概率的乘积,可以表示为:
P (A和B)=P(A)×P(B)。
2.24比如某次交货包含12个阀门,其中四个是缺陷品而其余为无缺陷品。则抽取2个无缺陷阀
门的概率(将第一个抽取的阀门替换掉之后再抽取第二个)的概率可以计算如下:
·因为四个是缺陷品,其余八个必然是无缺陷品。因此P(有缺陷)=4,12, P(无缺陷)
=8/12。
· P(阀门1无缺陷)=8/12=2/3;P(阀门2无缺陷)=8,12=2/3 o
·P(阀门1无缺陷和阀门2无缺陷)=P(阀门1无缺陷)×P(阀门2无缺陷)
=2/3 x2/3=4/9(即0.44)。
2.25一个结果的期望货币价值(EMV)以E(x)表示,可以用给概率赋予货币价值来计算。
·例如,如果一个高新产品挣得X美元的概率为P,那么期望的产品价值是$X×P
·如果有一种以上的可能结果,则结果的EMV即$E(x)是单个结果的期望价值之和。因
此,如果该产品挣得X美元的概率是0.4且挣得Y美元的概率是0.6,那么该产品的总期
望价值是:
$(X×0.4) +$(Y×0.6)。
概率分布
2.26有三种主要的和非常实用的统计分布,见表5.3。这种计算的基础是,针对当前数据的一个
样本(例如一个流程的输出)的发布(比例),关于该样本所构成其一部分的更广的数据组
(例如该该流程之输出的其余部分,或该流程的未来输出)能够作一定的预见性假设(基于
概率)。
表5.3概率分布
正态分布
2.27二项分布和泊松分布关注事件发生或不发生的概率问题,正态分布与此不同,关注的是概率
的范围以及一个事件发生的可能性。
2.28首先,收集连续的数据并形成一个频数分布:表明数据项落入特定“组距”或带宽内的频数。
举一个简单的数字例子,考虑下列有75位参加者的一个统计样本的频数分布。
2.29然后将频数分布数据图示在一个直方图中:是这些数据集中中心(集中于平均值)、离差(分
散度)和形状(相对频数)的一个快速直观的总结。使用直方图,可以从大量数据中分析
出其含义,否则用表格形式则很难把握。年龄的频数分布的直方图见图5.5。该分布的总频
数由这些长方形的总面积表示。
图5.5直方图(以相同的组距)
2.30一种常见的直方图形状是反映数据正态分布的“钟形”,大多数数据都落在中央的(最高的)
方柱内,频数(方柱的高度)在顶峰两侧会基本上对称地有所降低。这反映了在自然中或
在行业背景下数据一般相对高地集中于平均值:随着偏差越来越大,偏离“模数”的数值也
越来越少,仅有少数几个外围的极端值。可以将此表示为一个频数曲线:见图5.6。正态分
布曲线就是众所周知的“钟形曲线”。
图5.6钟形曲线(正态分布)
2.31在数学上可以方便地将直方图的总面积作为一个面积单位,并将此推广至“钟形曲线下的面
积”。曲线之下的总面积被作为一个单位,因此,一个变量的值介于一定极限之问的概率对
应于总面积的一个比例。例如,在图5.7中,the probability that value处于X1和X2之间的
值X的概率是面积A(阴影部分)。这也可以表示为:
P(X1<X<X2)=A
可以使用正态分布表查得这一面积,也可以用计算机软件计算得出。
图5.7应用钟形曲线
2.32但首先需要知道所研究分布的均值(μ)和标准差(σ)。已知了这些值,变量的值(X1和
X2,) 即可标准化:即,它们可以用它们与均值差别的标准差的个数表示。
2.33在绩效测量和改进中,可以使用直方图、频数曲线和偏离均值的标准差,来分析过程的输出
与设定的目标和规格之间的匹配程度和可信程度。因此,它是一个过程能力分析工具,用以
确定一个过程满足要求的程度和可信度。在上述例子中,比如说Xl和X2代表钢筋直径的
上限和下限。
·买方指定直径80mm,公差+I-2mm。Xl=78mm,X2=82mm。
·一个供应商的制造过程输出直径不等的钢筋,直径均值为80mm,标准差为1.5mm。从
该过程中输出的钢筋在买方公差要求之内的可能性如何?
·计算(或使用正态分布表)表明,该供应商的输出中约82%在容许公差之内。这可以作
为设定改进目标的基础。
2.34如下所述,统计过程控制在控制图上使用上控制限和下控制限,以表明该过程在生产中何时
偏离期望(规格或目标)达到不可接受的偏差水平。其发明者Walter Shewtlart教授认为,
在正反两个方向上处于偏离均值3个标准差(3σ)的控制上限和控制下限,在对一个错误
信号做出反应的风险与对一个正确信号不做反应的风险之问提供了一个经济的权衡,无论过
程的分布如何。
2.35如果一个过程是正态分布,99.7%的数据处于离均值(正负)三个标准差的曲线内。换言之,
数值位于+/-3个标准差之外的概率只有0.3%。因此,一个测量值位于该中心带之外意味着
过程发生了移动,或变得不稳定了,或失去了控制:产生了更大的变动性。图5.8表示一个
正态分布曲线的均值为69,以及+/-3个标准差的数值。根据概率定律,小于63.4或大于
74.6的过程测量值几乎不太可能,这表明该过程没有问题。
图5.8过程分布示例
2.36可以使用下列数值画出过程抽样数据的直方图:过程输出的尺寸,或每千件输出的缺陷品个
数,或服务响应时间。一旦画出直方图,使用者可以考虑客户期望(规格和目标)并分析:
·离散度或过程的分散程度。可以用垂直线在图上加上规格上限和下限(如在上述例子中)。
整个过程样本可能落在规格限之内(可以接受的变动性);也可能样本的极值落在上下限
之外,这种情况下表明过于离散(变动性)不能满足客户期望:必须采取措施使输出更加
始终如一。
·过程的对中(Process centering)。一个高度集中的分布更有可能使规格上限与下限之
间很窄,使一个过程对中(例如使用机器或工具设置)也许比降低过程的变动性(其根
源可能很多)更容易。设定目标值(或公称规格)并表示为分布图上的一条垂直线。该直
线落在曲线中间,而不是落在左边(大部分输出高于目标)或右边(大多数输出低于目标),
这时该过程即得到对中。
第三节统计过程控制
3.1 很多过程改进技术的目的是减少过程中的变化,例如,确保过程的所有输出尽可能完全一样。
3.2一种常用技术时使用控制图。控制图用手标出上、下控制限,界定可接受输出的界限。例如,.
为了符合规格,从制造过程中输出的钢筋会被要求直径在10.8mm到11.Omrll之间。在此公
差之外的输出将被拒收。
3.3因此,过程改进的关键问题是理解引起变化的“特殊”起因,这些根源可能迫使该过程失去
控制,由此造成输出的产品超出上、下控制限。
3.4如第四章所述,SPC是一项在生产早期阶段识别质量缺陷可能性的技术。它旨在:
·使用统计方法
·对各个过程
·实施控制
3.5对于任何制造过程的输出,不能期望完全的一致。即使用最精确和高度自动化的过程进行生
产生产,比如钢筋生产,也可以用足够精确的测量仪器检测出钢筋之间的差异。如果生产过
程工作良好,那么这些随机差异通常不会引起不安:只有用精密仪器才能测量出这些差异,
且它们可能在容许公差之内。
3.6如果过程失去控制,情况就不同了。也许切削刀具变钝了,或者机器需要调整。这种情况下,
偏离规格的变化可能非常严重,且甚至更严重的是不可预测的。正是这类错误可以用SPC
检测出,以便采取补救措施。在整个生产运行中重复测试输出样本,能够熟练使用SPC的
操作者就可以检测出何种变化模式表示出现了过程错误。
3.7这一原理比较简单。质量保证和,或维护专家确定过程是否以正确的方式在运行。操作人员开
始生产并以较短的时问间隔对输出采样检验。记录测量数据,并使用统计分析,建立对所有
输出期望的平均测量指标。确定测量指标的期望范围。如果对样本的测量值聚集在这一预定
的测量指标附近或平均值在期望的参数之内,那么该过程在控制之下。如果结果在预期的参
数之外,那么它们就失去了控制。
3.8这是SPC概念的强项,因为在这一阶段操作者可以暂停生产来发现和纠正错误。仅有少数有
缺陷的产品被生产出来,一旦错误得到纠正,即可重新开始生产。
3.9值得庆幸的是,要执行这样的任务,操作者不必是统计学专家!SPC大部分依靠计算机系统
使用控制图。在操作者最初几个抽样之后就可以确定控制限。首先质量保证团队已经确保过
程是在控制之下,因此他们提出整个生产运行所期望的可靠基准,随后就可以进行上述工作。
控制图可能各有不同,但操作者一般关注两个测量指标。
样本的平均直径、重量、长度等。
每个样本的变化范围(变化范围窄是所期望的,而围绕平均值变化幅度宽则是不好的信号)。
3.10样本的平均测量单位通常用符号 表示,而一个样本中的测量值范围用R表示。操作者
测量一个样本中的单位并计算其平均值( ),结果应当落在设定的限内,即围绕期望值的上、
下控制限。类似地,所计算的R值不应当超过期望值一定数值,由上下控制限标出。这如图
5.9所示。
图5.9 SPC图
3.11 设立了控制限,下一步是评估一个给定的过程是否处于控制之下:即它是否是随时间统计稳
定的。下列情况下,图中各点模式可以表明失去控制的情形:
·一个或多个点处于上控制限或下控制限之外(在均值任一侧+/-3个标准差)
·连续三个点中有两个在均值任一侧超过+/-2个标准差。
·连续五个点中有四个在均值任一侧超过+/-1个标准差。
·连续六个或更多的点持续增高或降低(表明一种趋势)
·八个或更多的点处于均值的一侧。
3.12如果发生了失去控制的情况,应当在图中圈上这些点,且这应当启动一个预定的和记录在案
的反应方案:例如与主管取得联系;关闭该过程或实施在线维修;隔离上次抽样以来所生产
的可疑产品(用以检验和纠正);调查、分析和纠正出现失控情形的根源;对纠正后的过程
重新抽样;记录(在SPC图上)所发生的事情。
3.1 3 SPC是在一定条件下应用的一项数学技术。它最适用于连续的和重复性的生产任务。它是
用于确保生产过程保持在控制之下的一项技术(在其正常精度水平运行)。日本制造商对该
过程所做的改良是,随时间逐渐达到越来越严格的公差。这可以带来产品一致性的渐进和可
持续的改进。
3.14可是,SPC有其局限性。对于非标准的、非连续的任务,特别是如果生产批量很低的情况
下,SPC不适用。如果生产过程在本质上不能达到稳定状态,SPC也不适用。另一个问题
是成本:应用所要求的在线测试也许存在很大困难,而这样做的成本也许远远高于其所带来
的价值。
过程能力分析
3.1 5 SPC的局限性之一就是它关注于确保生产过程保持在控制之下:即在其正常精度水平之下
运行。可是,很多情况下仅仅用“正常精度水平”不足以达到买方的要求,这时SPC没有
什么帮助。
3.16过程能力是衡量一个过程在正常运行条件下所能达到的一致性(不变化性)的一个指标。如
果已知一个供应商的生产过程的过程能力,买方就能够将此与他的容许公差(变化范围)进
行比较。如果该供应商的过程能力处于该买方的容许公差之内,假如该系统在生产运行中保
持在控制之下(可以使用SPC进行控制),那么可以满足该买方的质量要求。
3.17过程能力的测量涉及到将在过程处于控制之下时过程中发生的自然可变性与买方所要求的
公差之问进行比较。二者匹配的程度是过程能力指数。如果用t表示买方的可接受公差范围,
v表示在过程处于控制之下时过程的自然可变性,那么过程能力(p)可以用下列公式计算:
p=t/v
3.18如果t=v(买方的容许公差范围正好与该过程的可变性相同),则该指数为1。如果过程可变
性小于买方的容许公差范围(v<t:这是个好消息!),那么该指数的值大于1。如果V>t(坏
信息),则该指数小于1.
失效模式与影响分析(FMEA)
3.19失效模式与影响分析(FMEA)是一种用以确定产品失效的不同方式(模式)并评估每种情
况下影响严重性的技术。(有时用术语FMECA,即“失效模式、影响和严重性分析”的缩写。)
使用适当的数字参数,可以对不同模式根据其关键程度进行排序,将注意力集中到那些最关
键的领域。
3.20应用FMEA的最佳时点是在设计阶段,但在产品生命周期的其他阶段也可以使用。为了提
供基本数据,需要来自各个不同职能部门的输入,如营销、客户服务、设计与工程、采购、
运营及其他部门。
3.21进行FMEA分析,需要下列步骤:
·识别构成该产品的各组件。
·对于每个组件,列出可能发生失效的不同方式及每种的原因。
·对于识别出的每种失效模式,列出对该产品整体的影响。
·评估每种失效的可能性(P),从1(不太可能)到10(极可能)。
·评估每种失效的严重程度(S),考虑其影响,从1(不太严重)到10(极严重)。
·评估在客户使用该产品之前检测出失效的困难程度(D),从1(容易检测)到10(很难
检测)。
·用下列公式计算每种失效模式的关键性指数(C):
C=P×S×D
3.22 C的值小,表明该失效模式不太重要,即它发生的可能性较低,或者它的严重程度较低,或
者它具有在客户使用该产品之前被发现的特性,或者同时具备上述三条。如果C的值大,表
明需要立即加以关注。
3.23最后,在每种情形下都应当指出纠正问题的方法。在此阶段,应当明确所需的措施。如果纠
正措施简单且成本较低,则通常应当对所有情形采用。 另一方面,如果纠正措施复杂且昂
贵,管理层必须审慎考虑该失效模式的关键性,然后再决定如何做。
因果分析
3.24现在,我们简要讨论几个诊断流程故障和质量缺陷的技术:因果分析(cause and effect
analysis),因-果-因分析(cause-effect-cause analysis)和和“为什么”分析(why—why analysis)。
3.25石川馨(Kaoru Ishikawa)提出了因果分析图(也称为石川图货鱼骨图),可以通过头脑风
暴发现质量问题的原因,并对其进行图示和分析。该图表明了各种可能的原因与结果之间的
关系,有助于揭示问题的根源,如图5.10所示。
图5.10 5M鱼骨图(制造业)
3.26这种技术最初是由质量管理中发展出来的,现在常用作一种项目管理工具。在非制造业背景
下,常常使用项目的4P(政策、程序、人员和设备),而非制造业中的5M(即Machine,Method,
MateriaI,Manpower和Maintenance)。
3.27绘出基础图之后,可以对问题的主要根源进行延伸并作为分支。然后将这些分原因加到图上,
直到考虑了所有可能的原因。Maylor在《项目管理》一书中解释了如何将该技术用于向客户
交付软件延迟的问题,如图5.11所示。
图5.11石川图,鱼骨图用于交付延迟问题
3.28在Maylor’所举的例子中,延迟问题被分为四个丰要的原因,即团体管理(政策)、软件规格
(程序)、团队人员(人员)和硬件(设备)。对其逐一进行进一步分析,在原始图上添加分
支。在该例中,识别出的主要问题是软件规格,特别是由于在开发期间曾做过规格变更。
因-果-因分析(Cause-effect-cause analysis)
3.29因一果一因分析(或“吹泡泡”)是在很多不吲因素相互关联的情况下使用的一种技术。关键的
问题是确定问题的根本原因,而不在那些看似原因其实是结果上过多分散精力。
3.30该技术在本质上也是一种图示法,为分析提供一种视觉和沟通工具。首先列举问题中的已知
因素,用“泡泡”画出来。如果某个因素被认定为另一个因素的一个原因(或部分原因),那么
将这两个泡泡用箭头连接起来表示。箭头的方向是从原因指向结果。
3.31 识别出的关系类型如图5.12所示。
图5.12因-果-因分析图
(a) 因素A是因素B的原因;因素B是一个结果。
(b) 因素A是因素B和因素C的原因。
(c) 因素A是因素C各是因素B的部分原因。
上述每种情况下,因素A的改进都将带来该流程的改进。
“为什么”分析,五个为什么分析或“根本原因”分析
3.32“为什么”分析(Why—Why analysis)或称为五个为什么分析(5一Why analysis),可用于支
持因果分析和因一果因分析,确保将原因与结果区分开,并确保分析是针对问题的最终根源的。
如果问“这个问题为什么会发生?”,则可以得到一个原因;如果问“为什么那样发生?”,则会
得出一个根本原因。据说,只有问五次“为什么”,才能深入问题本质并了解最终的根本原因,
常常为管理实践和规范奠定基础。这可以使问题解决与持续改进团队跳出固有思维模式,来
处理根本原因而不是问题表象。
3.33一家持续改进咨询公司More Steam提供了用于某电器制造商的五个为什么分析表格示例,
如图5.13所示。
3.34考试中可能会使用下列更简单的模板:
五个为什么分析
故障模式:表层瓷漆缺陷
为什么#17 由于喷涂枪持有角度错误导致的瓷漆凹点(一种“橙皮”结果)。
为什么撑27新操作员没有得到充分培训。
为什么#3?缺勤太多干扰了培训计划。新操作员未被培训就上岗。……[等等】
临时措施:[措施……日期……】
持久措施:【措施……日期……】
评审:在三个月之内没有再发生?
图5.13五个为什么分析表格示例
第四节六西格玛方法
4.1六西格玛是统计学问题解决工具的一种专业运用,用以识别和量化浪费并且表明改进步骤。它
采用了宽泛的DMAlC方法(定义、测量、分析、改进、控制),目的是:
· 识别那些对客户而言关键的质量特性(CTQ)并对其进行排序。
· 定义绩效标准和关键变量的公差。
4.1 六西格玛是统计问题解决工具的一个规范的应用,用以识别和量化浪费并指出改进步骤,关
注于三个主要领域:提供客户满意度,降低周期时间和减少缺陷。这种质量测量和改进方法
最初由摩托罗拉在20世纪80年代提出,现在广泛用作一种变革管理的催化剂。它是基于朱
兰的统计研究成果(朱兰是质量管理的先驱之一,第四章讨论过)。
4.2六西格玛的目的是提高过程能力,或减小过程变化,以便使一个组织所提供的所有产品和服
务达到或超过客户期望。其名称源于统计学中用于度量标准差的希腊字母西格玛(o),标准
差衡量一个给定的流程偏离完美的程度。“西格玛个数”越多,一个流程越接近完美。通过测
量生产出的缺陷产品,你能够系统地消除它们,以追求零缺陷。达到“六西格玛”阶段的组
织,其流程控制已经相当严格,商业流程中只允许产生极少数的缺陷(每百万件中3.4个缺
陷),见表5.4。
表5.4西格玛水平作为过程控制的一种表述
4.3 Christopher和Rutherford解释了两西格玛过程和六西格玛过程之间的差别,如图5.14所示
(来源:www.martin-christopher.info/downloads)。
图5.1 4两西格玛和六西格玛之间的差异
4。4宽泛的六西格玛方法如下:
· 基于客户的输入与反馈(VOC,即“客户的声音”),识别那些对客户而言的“关键性质量
要素”(CTQ)并对其进行排序。
· 对关键变量定义详细的绩效标准和容许公差。
· 使用一些度量指标如每一定数量产出的次品数和该过程成功或失败的概率等,对真正的过
程能力进行统计上的测量。
· 对关键几个要素控制缺陷与变化(旨在零缺陷)。
· 使管理层和员工参与在该过程之中,以创建跨职能、以质量为中心的学习型文化。
4.5六西格玛的关键主题包括:
· 真正以客户为中心,以客户满意和客户价值来衡量改进。
· 科学的决策,以数据和事实为基础,以便能够有效地定义、分析和解决问题。
· 流程设计、改进和管理:流程的分析与优化是在质量和产出一致性方面取得可测量和可持
续改进的最有效途径。
· 主动的(而不是被动的)管理:管理者不是“救火”,而是专注于确定宏大目标、设定明
确的优先性、审视做事方式并提高过程能力。
· 无边界协作:强调内部和外部供应网络的跨职能参与、沟通和一体化。
· 追求完美——但作为风险、创新和学习的一个必要部分,要容忍失败。六西格玛鼓励原创
思维和从失误中学习。
4.6六西格玛关注于三个关键领域:流程改进,流程设计(和再设计)和流程管理。
流程改进
4.7关于流程改进(Process improvement),六西格玛使用DMAIC(定义一测量一分析一改进一控制)
法,概述如下:
· 定义:我们试图改进的是什么?一个严重的问题被识别出来,组成一个项目团队并赋予其
职责和资源来实现项目日标。确定要实施一个项目之后,应当准备一份“问题说明”来说
明该问题领域的具体细节。该说明应当用可测量的方式表述,作为项目任务范围和所需资
源与人力的基础。
· 测量(该流程):该流程目前的能力如何?流程产出中可见的平均值和变化性是什么?
· 分析:基于基本的想法,生成并研究各种推理以便确定出现缺陷的根源。使用流程图和因
果分析。通常首先确定各个阶段人们未按要求的行事方式,或人们未能确保有效控制的方
式。然后对各种根源进行排序并采取措施。
· 改进:通过对流程设计和实施变革(流程再造、简化等),从而消除所识别出的根源。
· 控制:设计和实施新的统计过程控制,以提高流程的可视性、控制未来流程绩效、维持取
得的成果。
流程设计
4.8流程设计(Process design)包括一个流程中所涉及的事件、活动或作业的排序,适当应用
技术与组织。流程设计有两个主要方面。
· 技术方面,包括作业的必要排序、技术的应用和流程所用方法的选择。例如,“排序”
(Sequencing)包括确定优先顺序和关键路径以及协调来自多种渠道的信息与工作流。
Robert Hayes和Steven Wheelwrright(《重建我们的竞争优势:通过制造竞争》)指出,
流程设计不仅仅靠技术能力和容量(机械、效率、灵活性、可靠性)来驱动,还受到诸如
技能要求、合规制度和现有系统等的限制与约束。
· 经济方面,由商业和竞争因素驱动,产生不同时期的流程改进压力。特别地,服务处理系
统的设计是由客户服务期望驱动的。
4.9 关于流程设计(或再设计),使用DMADV(定义一匹配,测量一分析一设计一验证)模型来达到“为
六西格玛而设计”(DfSS)。DMADV模型是一个五阶段流程设计(或再设计)模型,概述如
下。
· 定义:考虑到内部和外部要求,识别并设定新流程的目标。
· 匹配,测量:确定客户需求。适当情况下进行对标,并为达到这些目标制定绩效测量指标。
· 分析:对这些绩效测量指标进行分析并制定满足客户需求的新流程设计大纲。
· 设计(和实施):设计流程细节以满足绩效与客户标准,并实施。
· 验证:对设计执行情况引入控制,以确保达到了所述目标。
流程管理
4.10关于流程管理,六西格玛从根本上改变了一个组织的结构和管理方式。流程管理包括下列步
骤。
· 理解和确定各流程,珲解客户要求并识别流程的责仟人(内部的和外部的)。
· 对照客户要求和关键绩效指标,对绩效进行持续测量。
· 分析数据以监控和改善测量指标。
· 通过监控输入、转化和输出和对预料之外的变化做出响应,控制流程绩效。
选择六西格玛团队
4.11 六西格玛使用一批专家为组织基础架构提供基础,以支持该项目。一个典型的六西格玛团队
由下列人员组成:
· 盟主(Champions):懂得六西格玛并作为黑带导师的高层领导,与高级管理层进行互动。
· 导师(Mentors):推动项目并给予支持和指导的人。
· 黑带大师(Master black belts):经验丰富的、全职领导者,具有六西格玛的丰富知识。
他们在适当情况下提供建议、反馈意见、指导、项目计划建议和培训。
· 黑带(Black belts):质量项目的领导者,通常是全职的,直到项目完成。一般认为大多
数六西格玛项目历时在3到6个月。
· 绿带(Green belts):兼职项目工作,但常常在他们自己的领域或职能部门领导团队。
供应链中的六西格玛
4.12 Christoptler等人指出,六西格玛实践已经不限于在工厂之内。“与很多制造流程不同,供应
链流程常常针对时间进行测量(例如按时交货,拣选率等),而不是针对一些物理尺寸或质量
(例如拣选准确地、产品容许公差等)。如果我们应用六西格玛技术来压缩在时间方面的变化,
那么前置期就变得更加可靠,并可以降低安全库存水平。看来,六西格玛为创建更强健的供
应链流程提供了一个途径,可以降低供应链流程的不合规风险并由此生产出更可靠的和一致
的产出。”
4.13 Christoptler等人引用了福特公司客户驱动的六西格玛计划。在一个六西格玛项目中,福特
的分析人员在其中一个工厂测量了库存水平,发现一个月内变化20%。进一步调查发现,库
存波动的主要原因之一是在工厂的月台上零件的装货效率低下且不一致。采取步骤提高了月
台使用率并避免流程的变化,由于降低了库存,减少了未计划物料搬运引起的超时等,冈此
带来了每年370万美元的节约。
第五节持续改进
5.1 第四章我们论述了持续改进在全面质量管理中的重要性。尽管中基本上不是一个统计问题,
我们在此重回这一论题以便为大纲中所提工具和技术提供一些细节内容。
PDCA(戴明)循环
5.2如上面讨论六西格玛时看到的,流程改进关注于:
· 纠正所识别的引起变化、无效率或问题的各种原因,目的是提高流程输出的质量、一致性
和成本效率;
· 以迭代循环方式,追求持续的、渐进的改进。
5.3“计划一执行一检查一纠正”(PDCA)循环是一个流程改进模型,为持续改进提供了一个结构化
的框架,也称为持续改进循环。该循环是由质量大师戴明推广的,基于统计专家Walter·
Shewhart的工作。戴明最初关注于测量产品的偏差,目的是持续减少变化性,但该循环可以
通过下列重复性(迭代)步骤用于任何流程:
· 计划:提前为变化制定计划,并分析和预测结果(即收集数据,分析数据,评估问题,制
定可能解决方案,为引入首选解决方案制定计划)。
· 执行:实施该解决方案,在受控环境中小步实施。
· 检查:对该解决方案的绩效或该变化的影响进行测量。(这个阶段有时称为“学习”,该循
环因此也称为“PDSA”。)
· 纠正:为流程的标准化或改进制定进一步的行动方案。
5.4 由于戴明循环的灵活性,它可用于很多情形,包括:日常的个人和团队管理,问题解决,项
目管理,人力资源(和供应商)开发与改进,新产品开发,流程改进。
持续改进
5.5 Mullins在《管理与组织行为》一书中指出,“改善”(KAIZEN)是一个日本语的概念,是指
以持续演变为基础的全面质量管理方法,员工在某种固定的边界之内承担着相当大的责任。
这不是强调“第一次将事情做正确”,而是强调“下一次,将事情做得更好一些”。这一词语在日
语中意思是指在生活和商业实践中各个领域中实现持续改进的一种渐进的、有条理的方法。
在很多日本管理概念中都体现了“改善”理念,如全面质量管理,质量小组和协作劳工关系。
5.6“持续改进”寻求的是非间断的、持续进行的增量改变:总会存在改进的余地,例如通过消除浪
费(非增值活动)或者对设备、物料或团队行为进行的微小调整。从本质上讲,它是一个实
现变革的周期性方法,因为它也包含了为了未来学习和改进而进行的反思或评估。
5_7“持续改进”的一个基本的周期性方法如图5.15所示。你可以认为它是用于持续过程改进的“计
划一执行一检查一纠正”(PDCA)方法的一个变体。
图5.15持续改进循环
5.8持续改进在本质上也是一种“自下而上”的质量方法,因为它利用了来自与质量问题最密切
相关的那些人(操作人员与客户)的反馈、改进建议和想法。持续改进是基于团队的问题解
决方法,使用“改进小组”(或质量小组),来解决所发现的问题。对问题加以分析,生成想
法与建议,对建议进行实施,以一种结构化的方式应用工具与技术来弄清楚根源,并确定改
进方案。这可以使买方组织和供应商组织都广泛参与,通常也不需要大量的资金投资。
5.9使用持续改进概念常常涉及到针对流程优化的小的、渐进的改进。持续改进项目通常旨在以
最少的花费在短时间内实现显著的运作结果。为了发展供应商对持续改进概念的承诺,组织
一般选择一个相当简单但有很高首次成功可能性的项目,通过“小的成功”聚集动力。这有
助于持续改进的基本价值观,如自律和提高士气。
5.10小的改进的不断积累,可以带来重大收益,但持续改进在本质上限于关注现有系统和流程的
改进。有些情况下,也许需要激进的或“非连续的”思维,特别是当系统过时或从根本上功
能失调的时候。我们将在第六章论述一种主要的“非连续的”改进方法。
质量小组
5.11持续改进的…一种方法是运用质量小组(Quality circles),它也用作TQM的一个环节。质量小
组有时也用于指质量改进团队或自我改进学习小组。这种方法是20世纪60年代由日本质量
大师石川馨首先提出的。其基础是认识到工人的价值,反映了下列原则:参与型管理、人力
资源开发和问题解决。
5.12质量小组(QC)实际上就是来自组织中不同层级和职能的员工组成的一个自愿参加的小型团
队,定期碰面,讨论质量有关问题,分享最优做法,提出改进建议。质量小组的活动得到全
公司联络员和管理协调员的支持,常常接受一个执行委员会的政策指导。每个质量小组的活
动一般由一位指定的小组领导进行联络协调。
5.13为了追求过程改进,QC常常使用很多基本工具和技术。
· 问题解工具(例如流程图析,头脑风暴,石川图,因果分析)
·人力资源开发工具(例如领导技巧,沟通风格,指导和辅导技巧)
·参与式管理工具(例如协调、演讲和交付的技巧)。
5.14小组活动的基本顺序一般遵循下列框架。
· 问题识别、选择与分析:使用基木的问题解决工具。
·制定并评估各种替代解决方案,选择符合特定标准的最合适的解决方案。
·为所制定的解决方案制定行动计划。
·提交解决方案与行动计划,以获得批准与授权。
·实施:可能的情况_卜,在推出之前对该解决方案先进行小规模测试。如果该解决方案不成
功,重复该循环,直至取得成功的结果。
5.15质量小组对于它们所提建议的实施、执行和监督过程,可能承担、也可能不承担重要的职责。
可是,即便是作为讨论小组,它们也有着重要的优点:
·利用组织不同职能和层级的专长;
·改变雇员的态度,树立质量“拥护者”:工人变为“流程的负责人”,致力于持续改进。
·通过学习新技术,开发并释放工人的潜能
·改进关于质量问题的跨职能沟通和信息共享;
·让雇员参与到质量问题中,创造积极的和主动的工作环境
5.16必须认识到,质量小组法在欧洲和美国有成功也有失败。QC并非一个快速见效的解决方案,
抱有不现实的期望常常会带来失望。调查结果表明,常常由于下列原因导致没有成果。
·缺乏管理层的承诺与支持
·受到来自中层的抵制
·QC的运行超出了其有用的寿命
·缺乏灵活的人员和技能来满足不断变化的问题和形势。
持续改进协议
5.17可以在长期供应合同、关系宪章或伙伴关系协议中设立对持续改进的承诺,带有绩效测量指
标和改进目标(定期评审和更新)。
持续改进方法的好处
5.18渐进式的变革常常被用作一种主动的商业改进方法,它是在现有情况(现状)基础上在很长
时期慢慢建立起来的。因为它只是要求现实的、小的运作改进和消除浪费,因此可以采用“自
_F而上”的方式来实施,通过提意见、质量小组和自我提高计划让员工参与。
5.19这对于建立组织的学习和核心能力是一个特别有效的方法:建立组织对的变革的一般响应能
力(如对客户需求的变化,行业动态和文化变化)。
5.20渐进式改进方法:
·建立在组织内现有技能、惯例和信仰的基础_卜:变革可能更有效率、创伤较小、更容易赢
得接纳和承诺。阻力可能更小,不需要太多的管理投入。
·对环境的变化和反馈有灵活性和响应性,不断调整以使与战略保持一致。不用在有很大不
确定性的长期计划上浪费资源。
·保持一种持续进步的感觉,尽管有不确定性和困难。小的变革容易实现,可以触发(或有
助于实现)大的变革:小想法可以发展成人战略。这是持续改进关于学习和质量管理理念
的基石。
·员_T授权。小想法可以发展成大战略,因此组织内的任何人都可能成为战略家。持续改进,
以及实现小改进并带来大改进的能力,可以成为工作满意感和雇员与供应商承诺的一个巨
大源泉。
本章小结
·应当对照各种可能的标杆,对供应商绩效进行测量。关键绩效指标应当具有SMART特性。
·可以使用统计抽样来检验物品质量。通常需要用平均值和离散度量指标来描述物品的总体。
·常见的概率分布有二项分布、泊松分布和正态分布。
·统计过程控制旨在使用统计方法对生产过程进行控制。操作人员测量来自过程的输出并将
其与SPC图中设定的期望值进行比较。
·六西格玛是统计工具的一个应用,旨在提高过程能力和减小过程变化。
·“计划一执行一检查一纠正”(PDCA)循环是一个流程改进模型,旨在实现持续改进。质量
小组是这一领域的另一项技术。
自测题
括号内数字为参考答案所在段落。
1 列举供应商绩效测量可以对照的一些标杆。(1.1)
2 SMART目标是什么意思?(1.8)
3列举供应商绩效中所用的可能的成功要素和KPI。(表5.2)
4解释(a)简单随机抽样,(b)系统抽样和(c)分层抽样。(2.3)
5解释标准差是什么意思。(2.17)
6 SPC操作员通常关注的两个测量指标是什么?(3.9)
7什么是过程能力指数?它如何使用?(3.17,3.18)
8失效模式与影响分析中有哪些步骤?(3.21)
9六西格玛中DMAIC流程改进法是什么意思?(4.7)
10解释PDCA循环中的各个阶段。(5.3)
。
>>>更多章节请登陆本站CIPS学习社区查阅<<<
The End.
苏州采购与物流考服中心资料编辑部整理发布,十年来我们致力于打造互联网上最专业、最公益的供应链人学习平台,更多学习资源可访问www.szcps.net或关注微信公众订阅号:szcips 未经许可,禁止翻印,如发现互联网百度文库、道客巴巴、豆丁网等社区论坛上有本资料,可以及时举报,举报热线15366201980,凡举报核实无误者,赠100元奖励。
苏州采购与物流考服中心由"江苏省级采购与供应管理学历助学机构"、"江苏省级物流管理学历助学机构"、"中国采购与供应管理职业资格证书苏州认证分中心"、"中国物流职业经理资格证书苏州认证中心"、"CIPS苏州授权认证培训考试中心"、"IACCM国际合同与商务经理认证苏州咨询中心"、"中国大质量联盟苏州分中心"、"CPS/CIPS苏州考友会"、"苏州采购经理人指数研究成员单位"等多个供应链学习品牌构成,作为苏州供应链学习资源网发起单位-十年来,我们与广大学员致力于打造互联网上最专业、最公益的供应链人学习平台,更多学习资源可访问www.szcps.net或微信公众订阅号:szcips
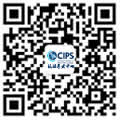